Following midsummer, the Oodi worksite is at a turning point, as both the roof structures and the works on the frame are almost ready. The first roof elements will arrive at the site during June.
“The steel frame of the building will be ready as planned by mid-July”, state YIT’s site manager Mansoor Ardam (left) and senior site manager Tero Seppänen. The construction site office screen behind them shows a live image of the entire Oodi site from above.

As the message on Kansalaistori says, Oodi will become the second living room to its visitors. For now, the rain still falls free on the living room floor, but one by one, the white steel structures on the third floor are being covered by a roof and surrounded by the glass facade panels.
“The roof is made of wood: it consists of laminated veneer lumber elements with a bitumen felt surface. The thermal insulation, for example, is built into the elements, which makes them almost one metre thick. The slightly curved shape of the roof is created during the installation of the elements, which are cut to shape at the factory”, Mansoor Ardam says.
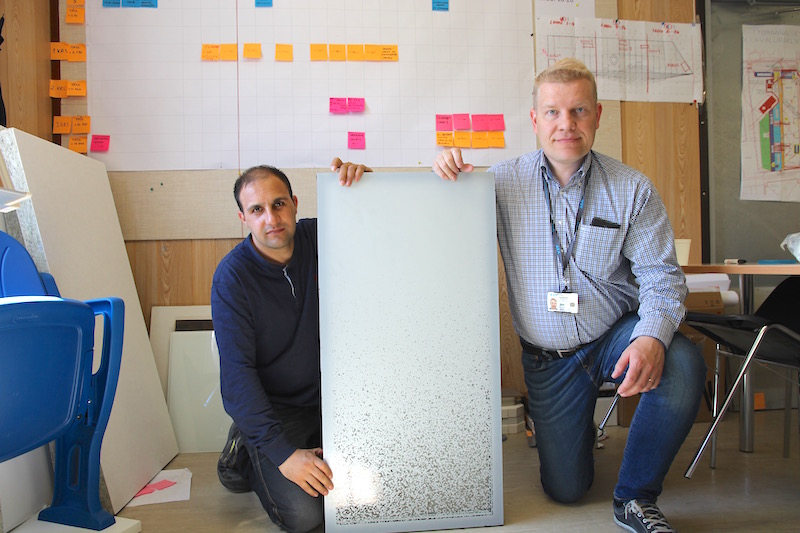
The facade on the third floor is entirely made of glass. A model piece of glass represents the visual idea of the third floor: from the top, the glass is entirely white, turning clearer little by little towards the bottom. Or, as Ardam creatively explains, it has a solid cover of snow up high, with snow falling downwards, before finally the view clears. Perhaps the thought of snow in the middle of summer is what made the men so serious?
First, the roof must be made steady
A fair amount of jangling could be heard on the Oodi site around midsummer. The new soundscape comes from the tightening of the white steel structures of the roof.

During installation, the roof beams were left slightly loose, so as to give in when necessary during assembly. The joints were later tightened one bolt at a time. The installer, working from a manlift, used an impact wrench, which caused the clattering heard in the surrounding area.
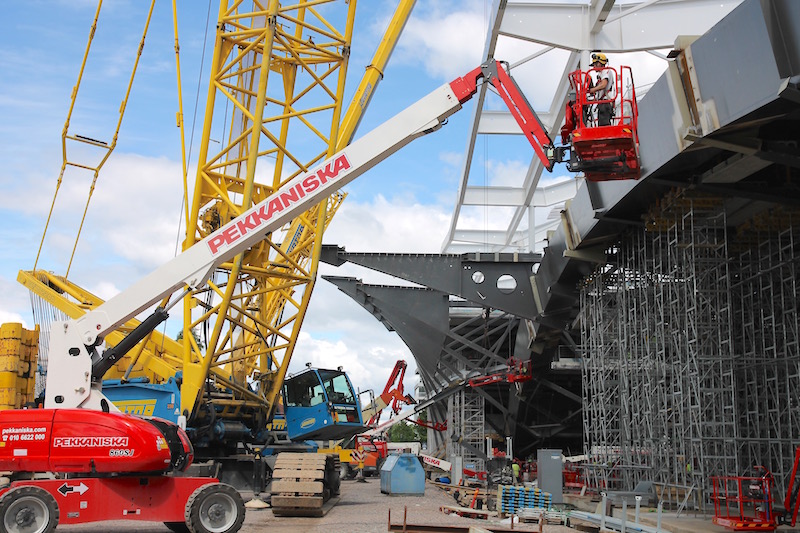
Due to the work being done on the roof and balcony, lately the front of the building has been bustling with cranes and manlifts. The largest crane, the 300-tonne Havator tracked lattice boom crane, which runs on caterpillar tracks, will soon have finished its job. The blue-and-yellow Havator came to the site in January for the installation of the steel arches that support the building, and it has also been used for lifting the steel roof parts. The Havator will be dismantled in July.
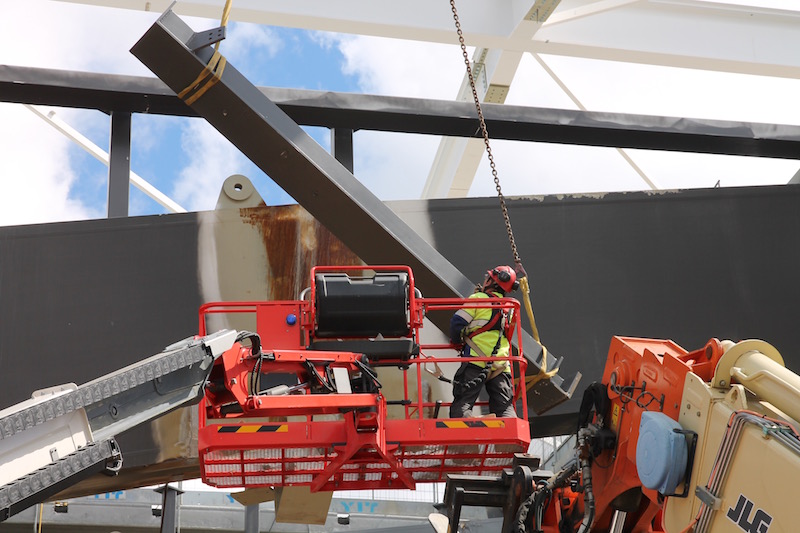
A balcony, which will be open to all visitors, will be built on the west side of the library, towards Kansalaistori. The steel gratings to support the balcony were installed in the middle of the building in June. The beams rose lightly on the crane’s chains, but brawn was needed to guide them to a suitable angle to be attached.

At the moment, a whole jumble of support towers stand under the steel arches, supporting the casting moulds above them. The moulds and support towers can be removed once the horizontal concrete vault has been cast and has dried enough to support the structures. The concrete cast-on-site vaults will also play a part in supporting the steel arches.
The even floor is actually curved
Most of the floors of the library are made from hollow-core slabs and fields formed from them. The hollow-core slabs have been used in both public and residential buildings since the 1970s, as they are a fast way of creating large surfaces.
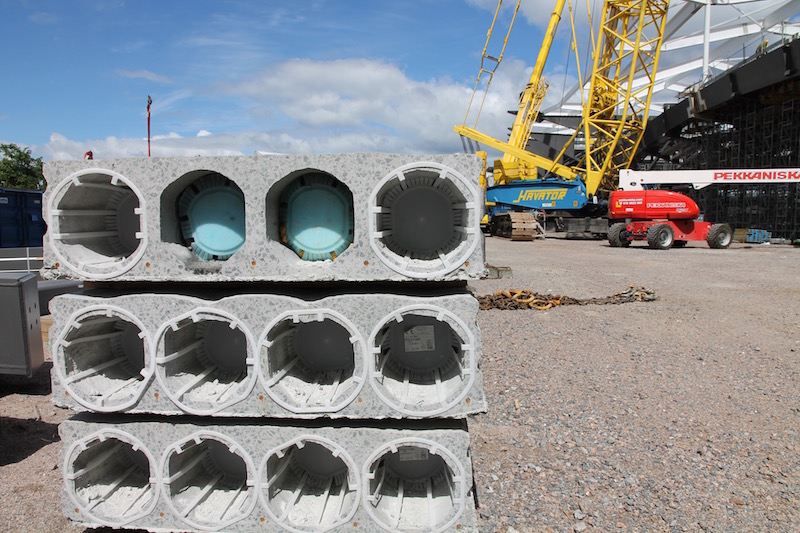
As the name suggests, hollow-core slabs are hollow, containing longitudinal cavities which make the slabs significantly lighter than solid slabs, even though they are made of reinforced concrete. The hollows can also be used for electric cables, for example. A pretensioned steel braid is running along the bottom of the slabs, which allows the slabs to be tensioned to increase their load bearing capacity.
“The tensioned cables make the slab curve a little. Even though the fields of hollow-core slabs look even, they are actually slightly curved”, Tero Seppänen explains.

Almost all of the hollow-core slabs are already in their places. The field of slabs that form the base of the upper floor also function as the ceiling for the lower floor. The seams of the individual hollow-core slabs are now being cast to make one big field.
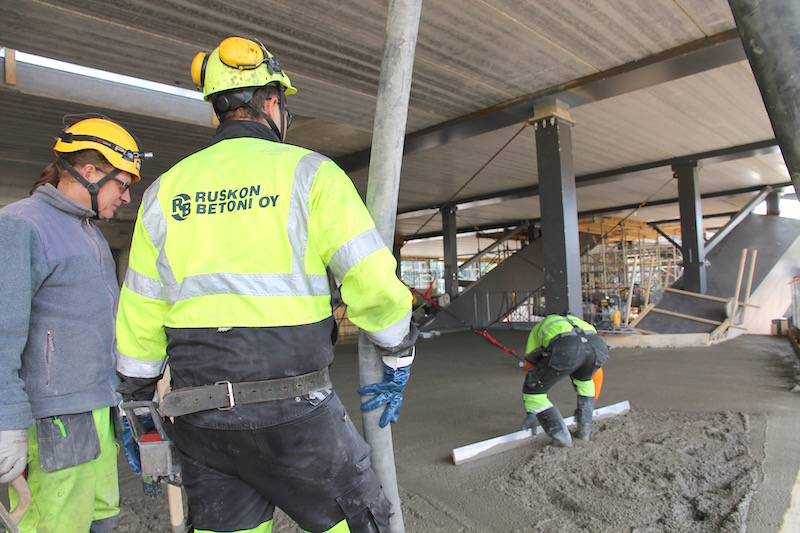
The floors are already being cast in the north end of the building. Here, the floor of the ventilator room is being levelled after concrete casting. In addition to the basement floor, there are ventilator rooms on the 1M level.

Building engineering work in the basement has proceeded smoothly. 90 per cent of the work on the main pipelines is already done, and the installation of the ventilators is well underway. Various pipes will soon be led to the upper floors in shafts. ARE’s electrician Aarno Lehtinen (left) held a meeting with YIT’s site manager Janne Kurikka and site engineer Ville Nevala in the construction site office, because the installation of the cable trays is ongoing.