The first roof elements have been erected in the northern end of Oodi. Piecing them together has been a giant jigsaw puzzle of rectangles and triangles, but it isn’t the lightest of jobs: the elements are 12 metres long and almost a metre thick. Their widths vary, but they all weigh thousands of kilos.
“We’ve only been able to bring two or three elements at a time to the site. The largest of them weigh eight tonnes,” says YIT’s senior site manager Tero Seppänen.
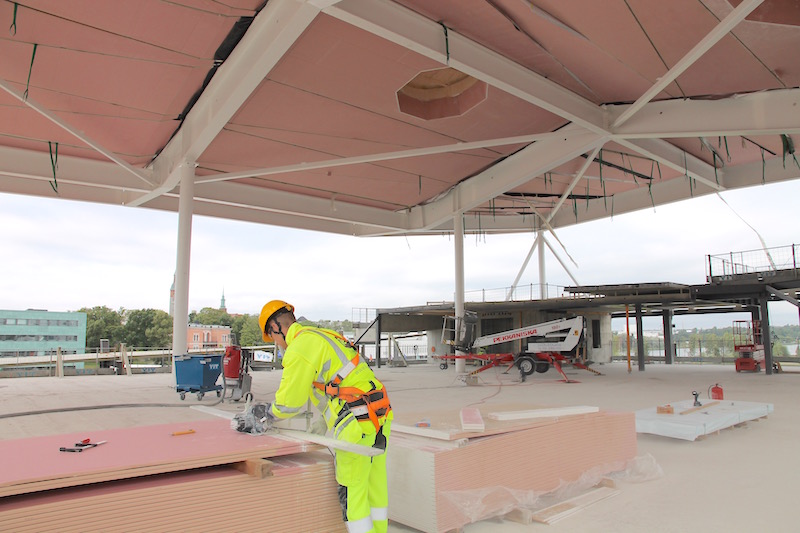
In late August and early September, a pink gypsum board was installed onto the elements, to function as fire retardant. The gypsum board will later be covered by the ceiling. At the same time, an architectural structure typical of the indoor area of the northern end, the balcony which can be seen in the background, was being built on the third floor.
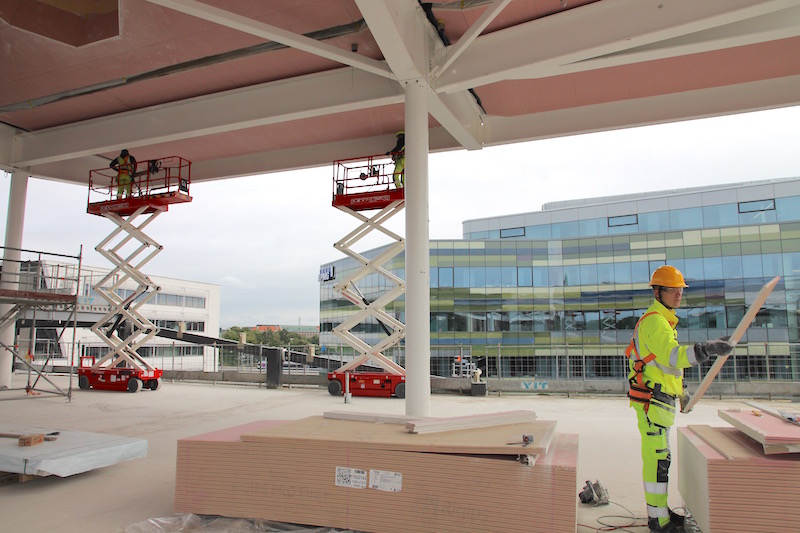
The roof elements were lowered into the supports waiting in the steel structures and screwed into their places. The Estonian Timbeco Woodhouse Oü was responsible for manufacturing the elements, and has now started installation work. The elements were cut to shape at the Timberpoint Oy factory in Loviisa.
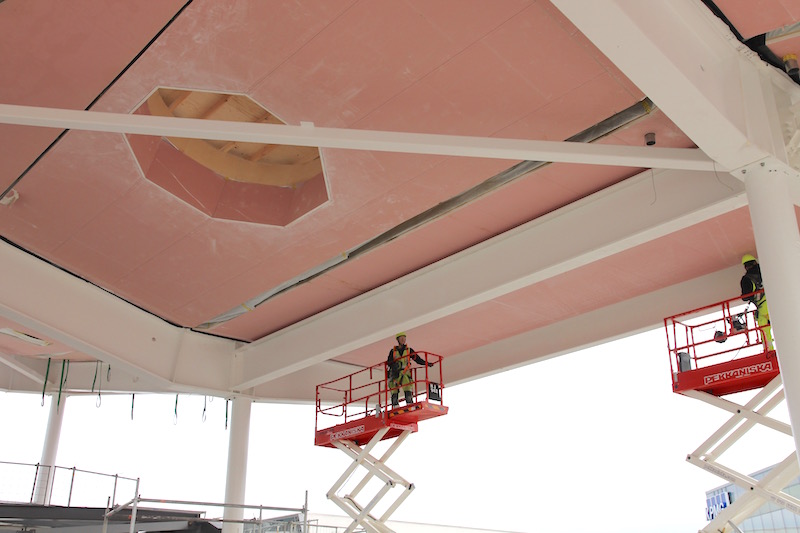
The elements were prepared in detail: places were even prepared for the skylights, such as the octagonal recess in the picture. In the seaming phase, the long sides of the elements are filled with a special urethane foam, and the short sides with mineral wool. It must be ensured that the top part of the seam is not too tight, because the wooden structure of the roof must be able to breathe.
Separate drainage wells on the balcony
The balcony is now waiting for the surface work, i.e. the concrete casting and waterproofing, to start. After those are finished, the surface tiling and wooden upholstery can be put up.
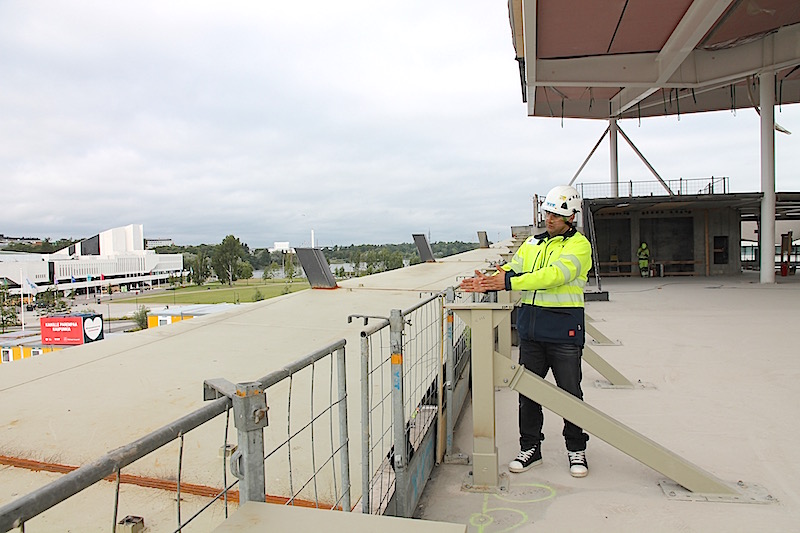
In order to prevent the balcony from becoming slippery, electrically heated drainage wells are installed within the structure. They will not freeze in the winter, allowing water to run off the balcony quickly.
On the third floor of the library, preparations are being made for the installation of the glass facade panels. Support structures for them are being built in the northern end. YIT’s site manager Mansoor Ardam shows the supports behind the balcony, where the floor-to-ceiling glass panels are to be installed.
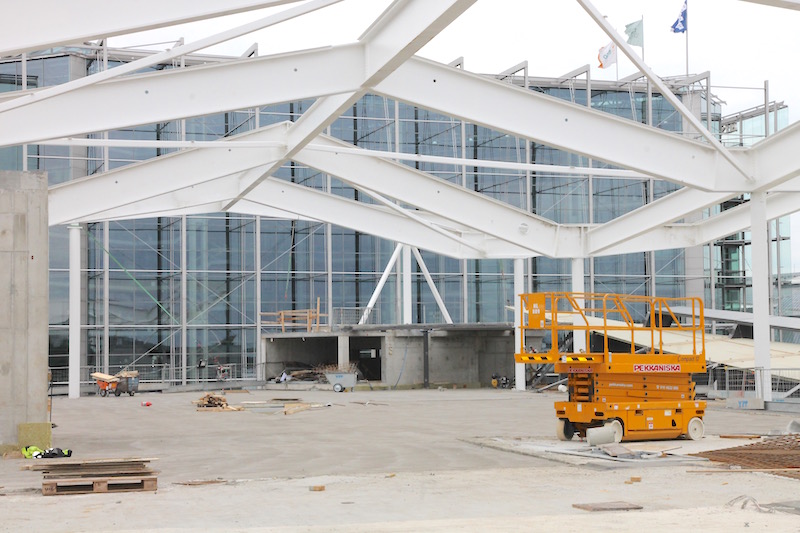
Casting the final part of the concrete floor on the southern end of the third floor in late August proved to be quite a task. The casting had to be done in one go, which took from 5 am to 8 pm. Over 200 cubic metres of concrete was used for the end part.
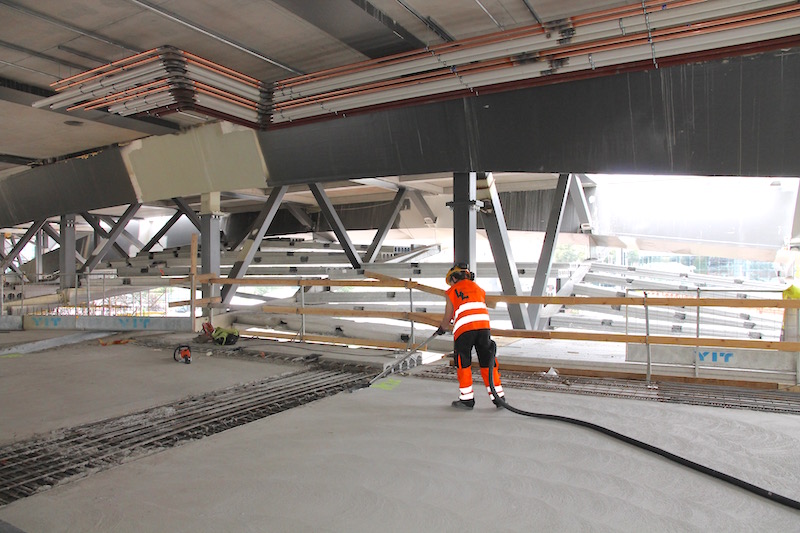
Floor casting is done on the second floor, but the fields of hollow-core slabs on the sitting area, which rise in steps, will be completed by stairs which will be cast in place. Concrete dust was vacuumed from the area from time to time.

Here, supports are being installed for the wall structures on the second floor, where the partitions will soon be built. Ceilings and floor surface materials will also soon be installed.
Final tightening of the anchoring cable
The work on the frame has now come so far that the anchoring cables running in the bull blocks of the steel arches which support the library could now be tightened for the third and final time.
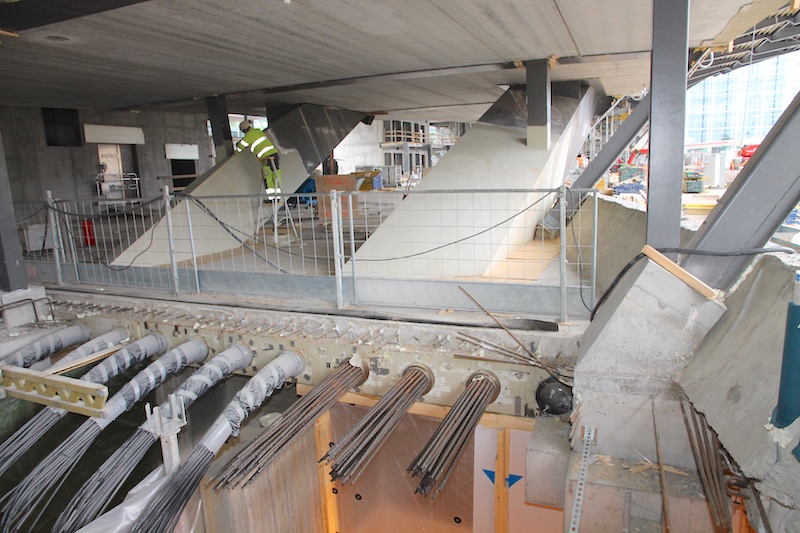
This will bring the bridge arches to their full bearing capability. The picture shows the northern housing structure of the arches, along with its steel slabs.
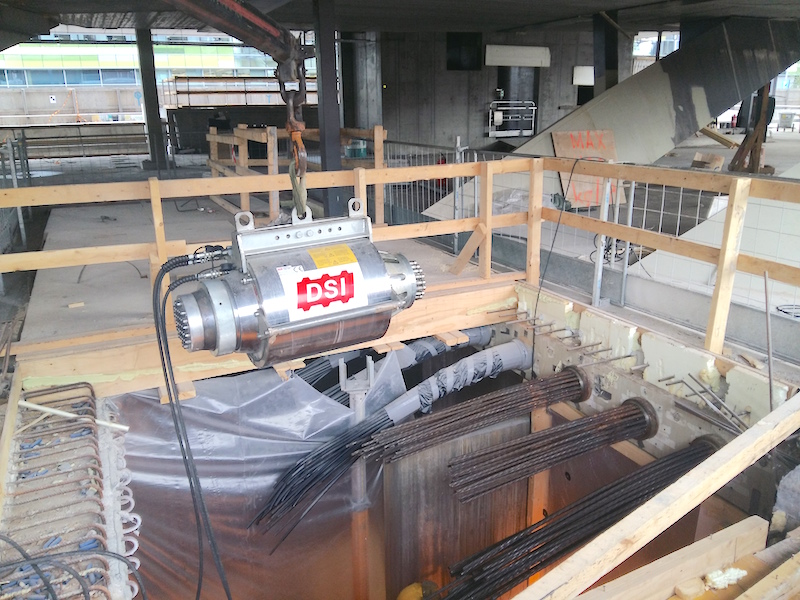
The cables were tightened using a hydraulic jack, of which there are only two in all of Europe. One of these was borrowed in Finland for the use of E.M.Pekkinen Oy, who performed the tightening, for three days. After the tightening was done, the cables were cut off and the ends of the cable bunches plugged. Photo: Mansoor Ardam.
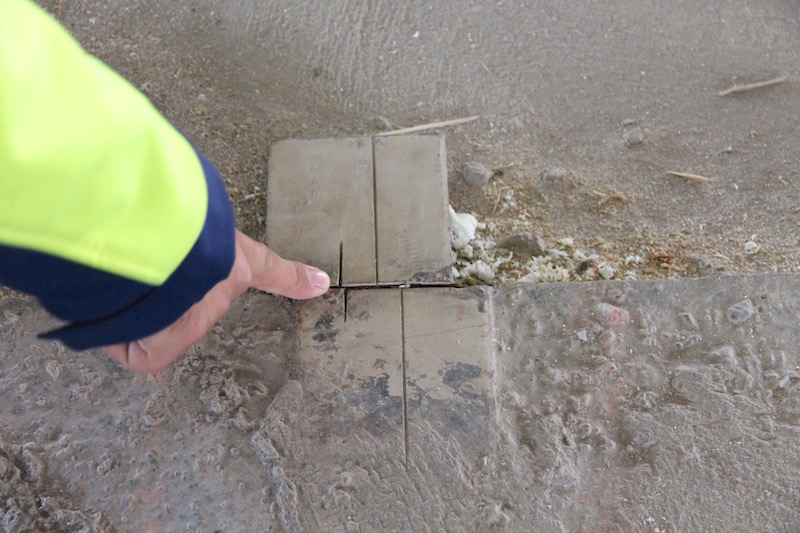
Site manager Mansoor Ardam wanted to find out how much the bull block moves during tightening. He placed two steel patches on the floor on either side of the seam. Using lines drawn, he noticed that the tightened slab had moved one centimetre compared to the untightened one. The expansion joints, which were previously left open on the first floor, can now be closed.
Floating movie theatre floor
Floor casting is a hot topic also in the first floor library movie theatre.
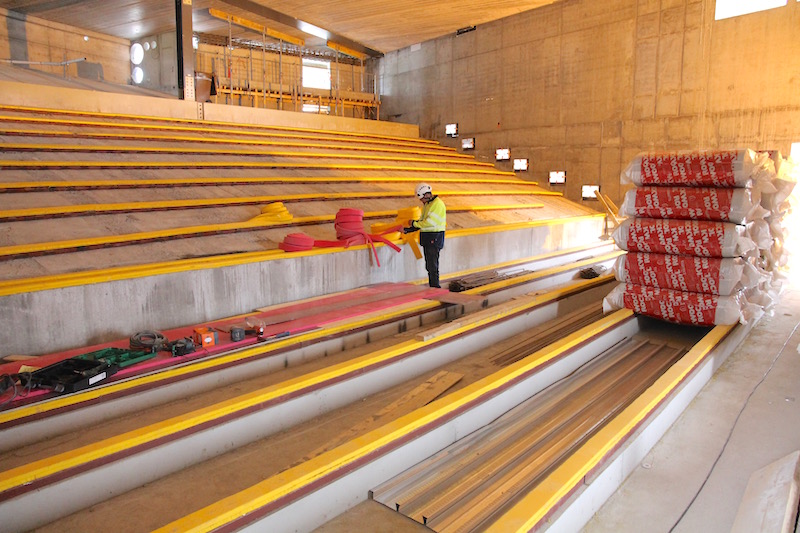
Due to acoustics, floating concrete slabs are used in the frame structure of the movie theatre. The yellow sound-absorbing Sylomer isolator separates the surface structure from the frame structure, preventing the sounds from the theatre from being conveyed to other parts of the building through the frame.
Interior materials on the drawing board
As the frame and floor castings are finished, the site can gradually turn its thoughts towards interior materials. Various brochures and samples on floor materials, for example, have gradually found their way to the construction site office.
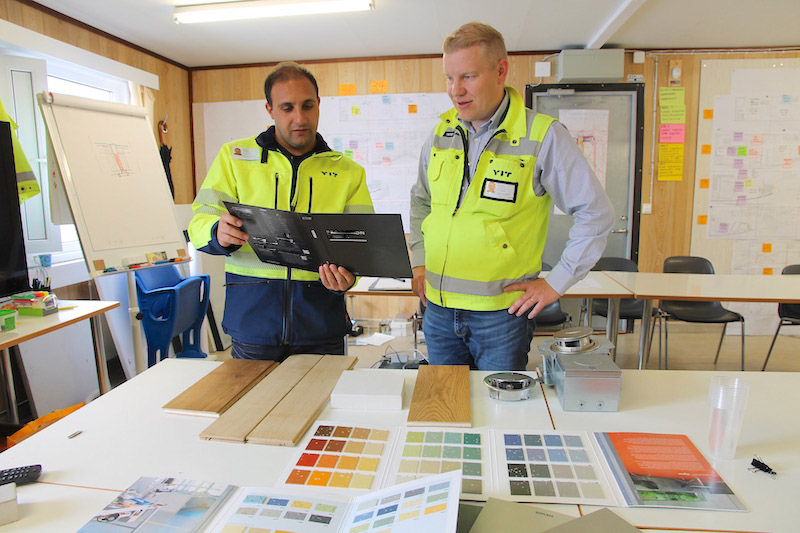
According to Mansoor Ardam and Tero Seppänen, no decisions or agreements have been made yet, but preliminary discussions with various suppliers have taken place.
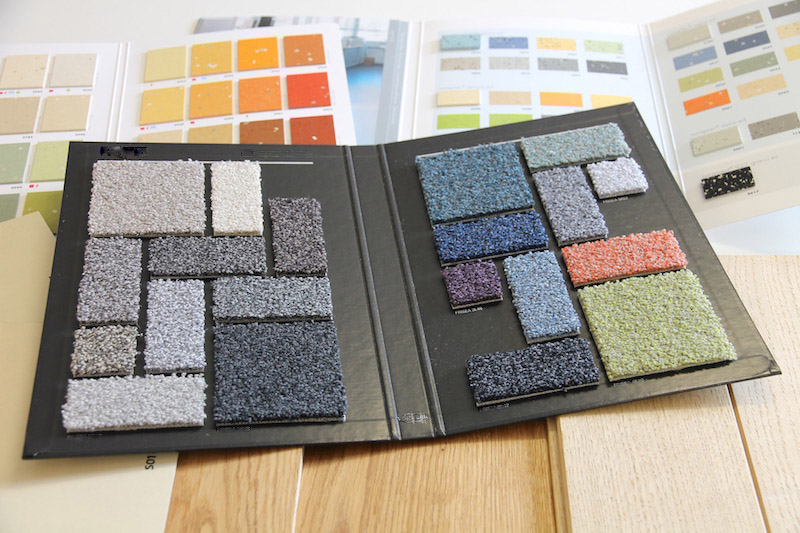
The interior materials will generate lots of discussion, with so many materials and colours to choose from. Practicality should meld with the visual values, and the overall look should please the public.
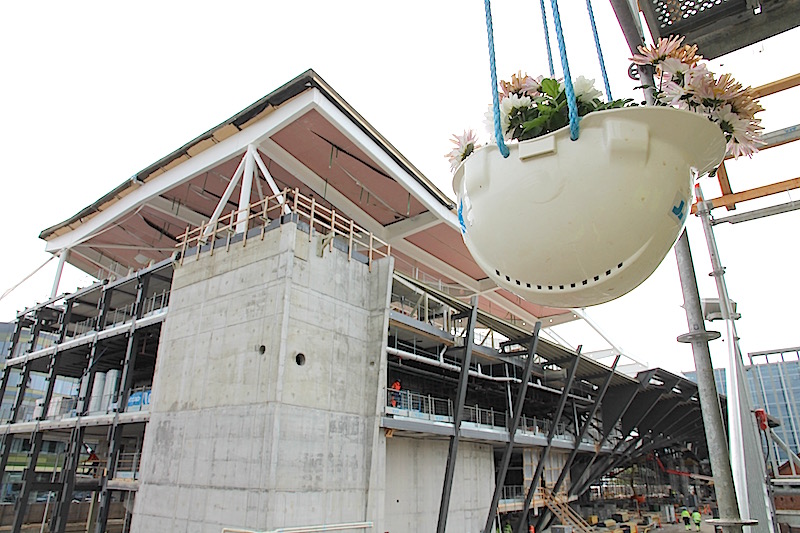
Summer’s still here, at least if you ask the hanging flower pot helmet. At the moment, approximately one hundred people are working with the construction of the library. The summer trainees were so good that YIT hired them as workers paid by the hour. As studying and work are combined, so too are theory and practice.